Content
How to build fabric first

The UK won't meet its legally binding targets of net zero by 2050 without near complete decarbonisation of the existing building stock and embracing a fabric first approach.
Many organisations are calling for a national retrofit strategy. Demand for retrofit, fabric first and related green skills is growing. We need an immense expansion of trades and professionals to meet this challenge.
Policy isn't changing quickly but the industry’s demand is, so it is time that you had the opportunity to take your first steps in learning about sustainable approaches to building and have a go at implementing them yourself.
This is why we have delivered Low Carbon Learning: Fabric and Structure online and practical learning modules to support the built environment industry in Scotland to work towards achieving net zero. The programme aims to show how you can use fabric first principles to meet current and future energy efficiency requirements and work towards achieving zero carbon and near zero energy homes.
By best utilising your building materials, products, and component parts, you can construct net zero buildings. To get you started, let’s have a look at the fabric first approach.
What is a fabric first approach?
Fabric first means optimising the performance of the components and materials that make up the physical matter of your building, including the walls, the floors and the roofs – improving them, optimising them and making sure they're working as hard as possible, even before you consider further systems such as heating or renewables.
Fabric first principles are about maximising air tightness and optimising solar gain, increasing levels of insulation in the fabric, optimising natural ventilation, and using the thermal mass of the building fabric. This approach to designing aims to minimise the requirement for heating and cooling of the property. Fabric first requires the design to be looked at holistically to establish both the thermal performance of each individual component and how it will function as a whole when installed.
Whether your project is new build or retrofit, there are things that you can do optimise your building’s fabric and structure.
There are many other principles and methods that feed into the holistic fabric first approach, including using carbon accounting in projects, choosing to use sustainable materials such as mass timber, and insulating your build with circular materials.
Carbon Accounting
If the fabric first approach to construction and refurbishment projects contributes to reducing emissions, carbon accounting enables us to take stock of it. This can be a good place to start with exploring the fabric and structure of a building.
The term carbon accounting means calculating the carbon footprint of a building a structure or even a business.
Buildings have a huge impact on carbon emissions. In 2020 CO2 emissions from the operation of buildings increased to their highest level ever - around 10 gigatonnes or 28% of total global energy-related CO2 emissions. If you add emissions from construction into that, the share increases to 38%.
The current business model of construction is one of the maintenance, modification and replacement of buildings and infrastructure. This is a major contributor and a significant producer of waste. There are ways we can improve this.
If you want to build yourself a new home, which material do you think has the lowest CO2?
The answer depends on a lot of factors: if the material is newly produced or recycled, where the energy to harvest or process the material came from, how far the components needed to travel to be able to produce material, and what the lifespan of the material is.
A brick may last more than 100 years. Many modern concretes on average last between 50 years. You don’t need to rebuild and reuse resources when using a longer lasting material, so in this example, the long-term emissions from the brick is better than the concrete.
For materials and buildings, one of the most significant considerations is its embodied carbon – what it’s emitting before it’s built, from its production through to its transport.
To be able to harvest wood, for example, you need to plant trees, take care of the trees and then harvest them, process the timber and transport it for production or construction. And all of this goes into the carbon calculation before the material has even reached site.
In this case the wood is far more sustainable when the final construction site is closer to the forestry that the wood is being taken from. If you use the materials locally you will always have a better emissions outcome. Furthermore, if you're reusing a material, the emissions go down even more drastically.
The 5 Rs
For simple guidance on these principles, try following the 5 Rs: Refuse, Reduce, Reuse, Repurpose, Recycle.
Refuse to invest in unsustainable materials. Try to keep the essentials then try to reduce those materials to what is actually needed. Also try to look for materials that are going to become waste from another construction and reuse them if possible. If you can’t reuse, look at repurposing items from other projects. An example of this is taking the doors of an old building and turning them into tables. In this way you're repurposing the material by changing its use but still making it functional. The last option is recycle. You need a lot of energy and a lot of resources to process a material so it's always best to keep it as the last resort to try to minimise this energy and cost investment.
Overall carbon accounting is fundamental. But as you have seen, what we put into a building means a lot for its sustainability. Materials like mass timber could be great way of driving a low carbon footprint.
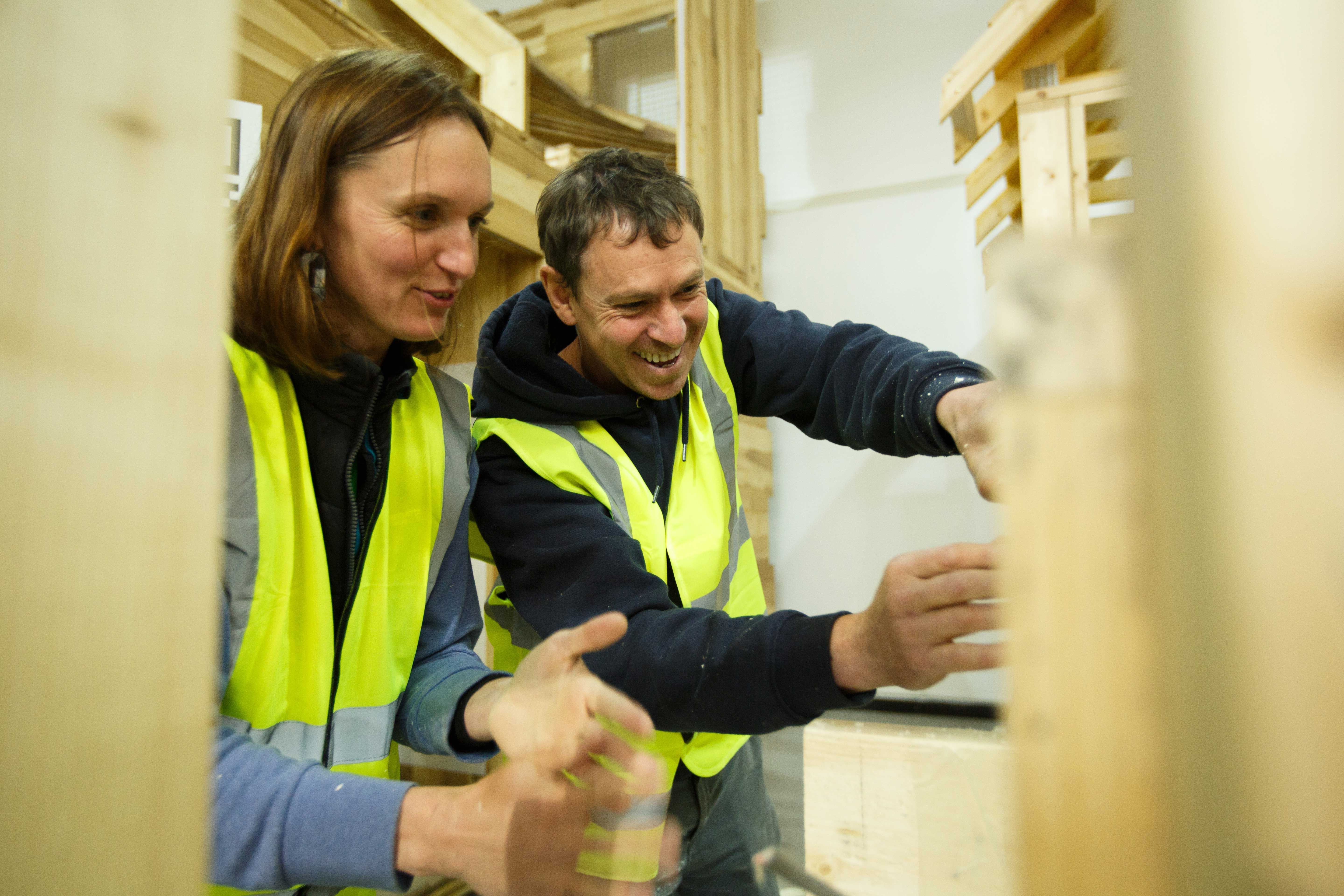
Mass timber
A lot has changed in the world of mass timber.
The general concept behind mass timber is to take a lot of small pieces of timber and connect them together by gluing or nailing them to act as one member.
In terms of the benefits of using solid timber in construction, it's a renewable material and is easy to work with, easy to adjust on a construction site and you can easily modify it.
It has amazing strength-to-weight ratio which when compared to concrete or steel makes it the perfect material for offsite construction, such as using mass timber systems.
Cross-laminated timber (CLT) and glue-laminated timber (GLT) are the most commonly used mass timber systems. The basic concept of CLT is to have a lot of timber boards (lamellas) slide down next to one another on a press. Then the next layer is glued to the previous one perpendicular and then another layer on top. You can build it up to nine layers. Typically, however, it is used as three-, five- or seven-layer systems. It is very commonly used as walls floors or roof. In the BE-ST factory usually we manufacture three-layer cross-laminated timber which can be adjusted to have 60-minute fire resistance.
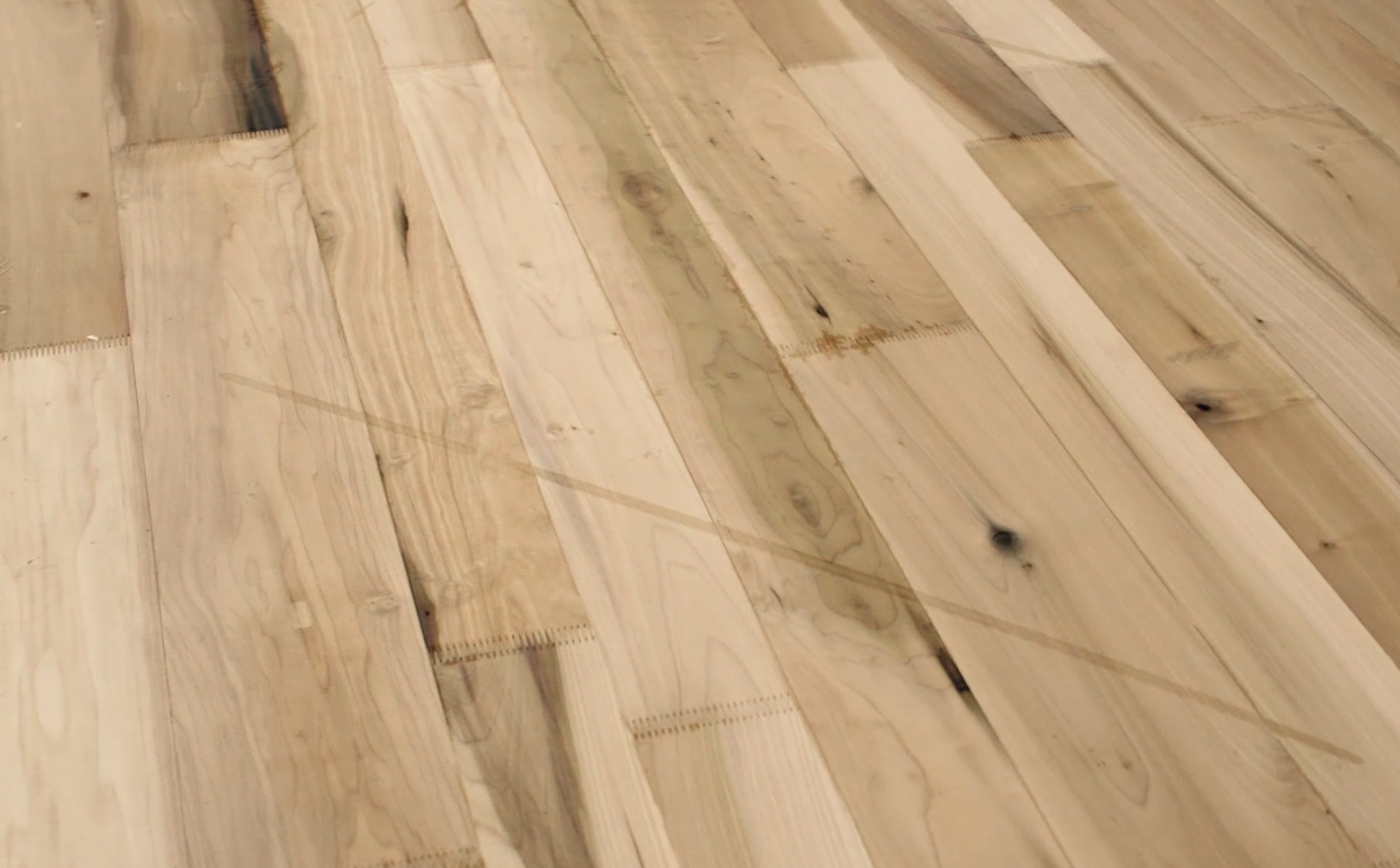
The environmental impact of using timber in construction is huge.
There is a process of carbon lockup when timber is used for construction. Trees suck up carbon from the atmosphere when growing and this carbon is locked inside when they are used for building, instead of released when left to rot. Every time we use timber we also avoid using concrete or steel so we have an indirect gain in lowering carbon emissions.
On top of all this, timber can be locally grown. This decreases transport, so every structure made with timber would have already have a lower carbon footprint than methods that require imports. If timber is homegrown the transport cost will be lower and it will have a quicker delivery time. At BE-ST we investigate and test homegrown mass timber products, usually British spruce as it is affordable and accessible and Scotland has got a lot of it. Homegrown mass timber would also boost the local economy and potentially create new workplaces. Up until very recently all of the mass timber in UK was made from imported timber from Europe and Canada. BE-ST is working to make a step change in this area through Transforming Timber.
As a contractor working with mass timber on site, one thing to bear in mind is to not use membranes that seal in moisture. One challenge observed during our Q&A session was related to mass timber and moisture damage. Contractors who have not used mass timber before might use membranes that seal in moisture into the panel and cause technical problems.
Still the opportunity for mass timber as part of a fabric first approach is undeniable, especially as part of a holistic look at a building’s structure and embodied carbon.
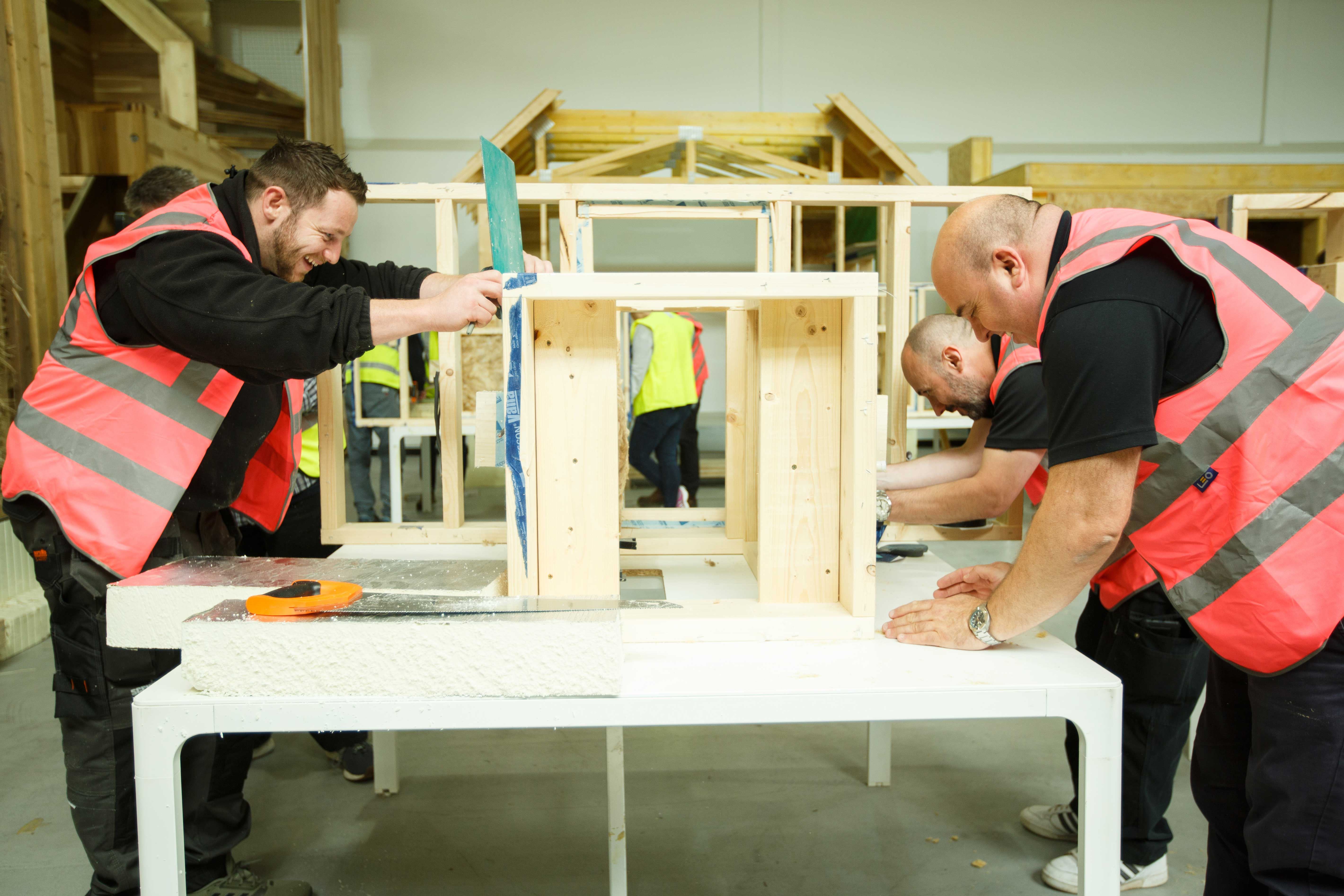