Content
Dandara: Building a Scottish supply chain
Researching the possibility of a Scottish Passivhaus standard
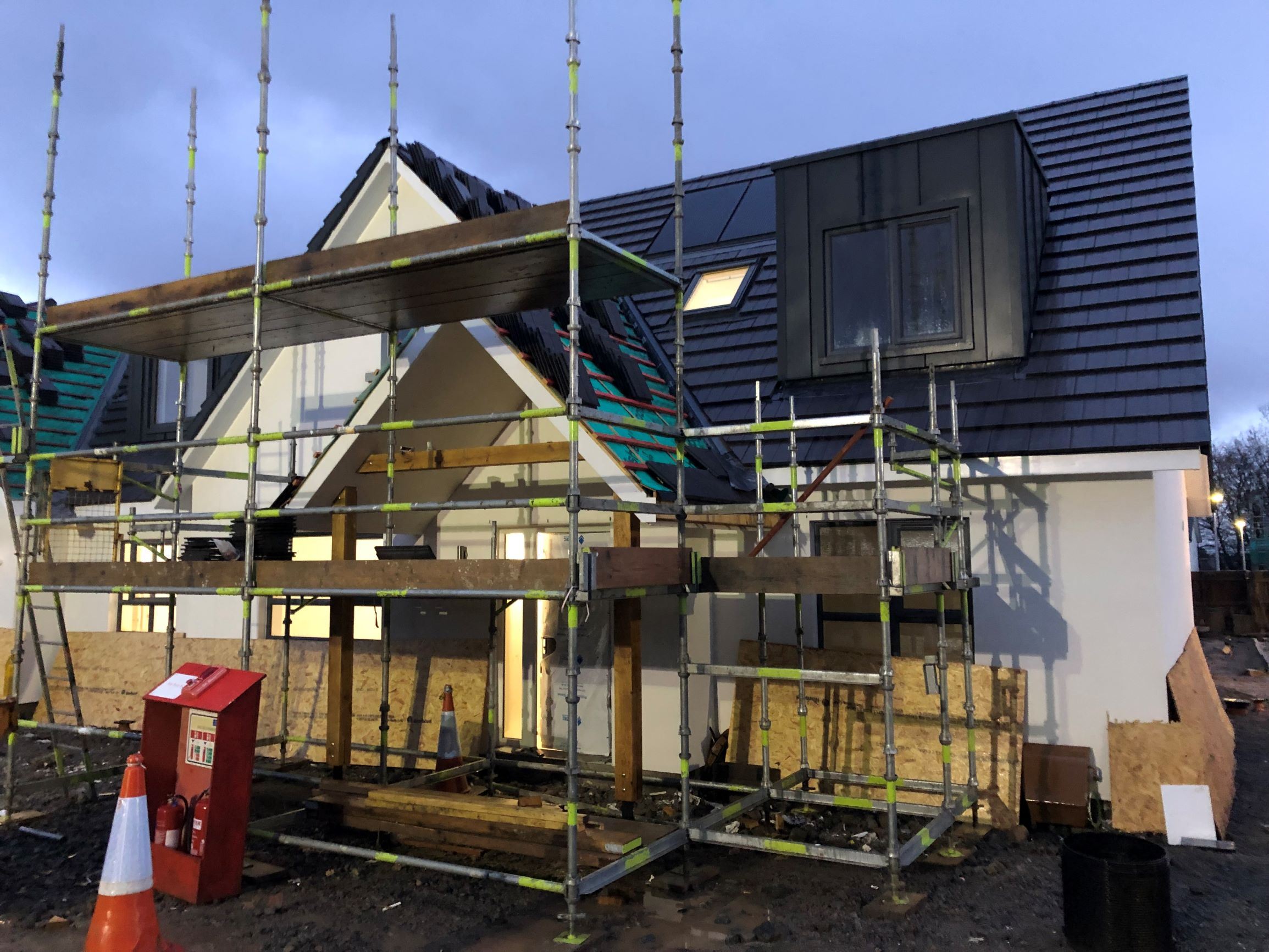
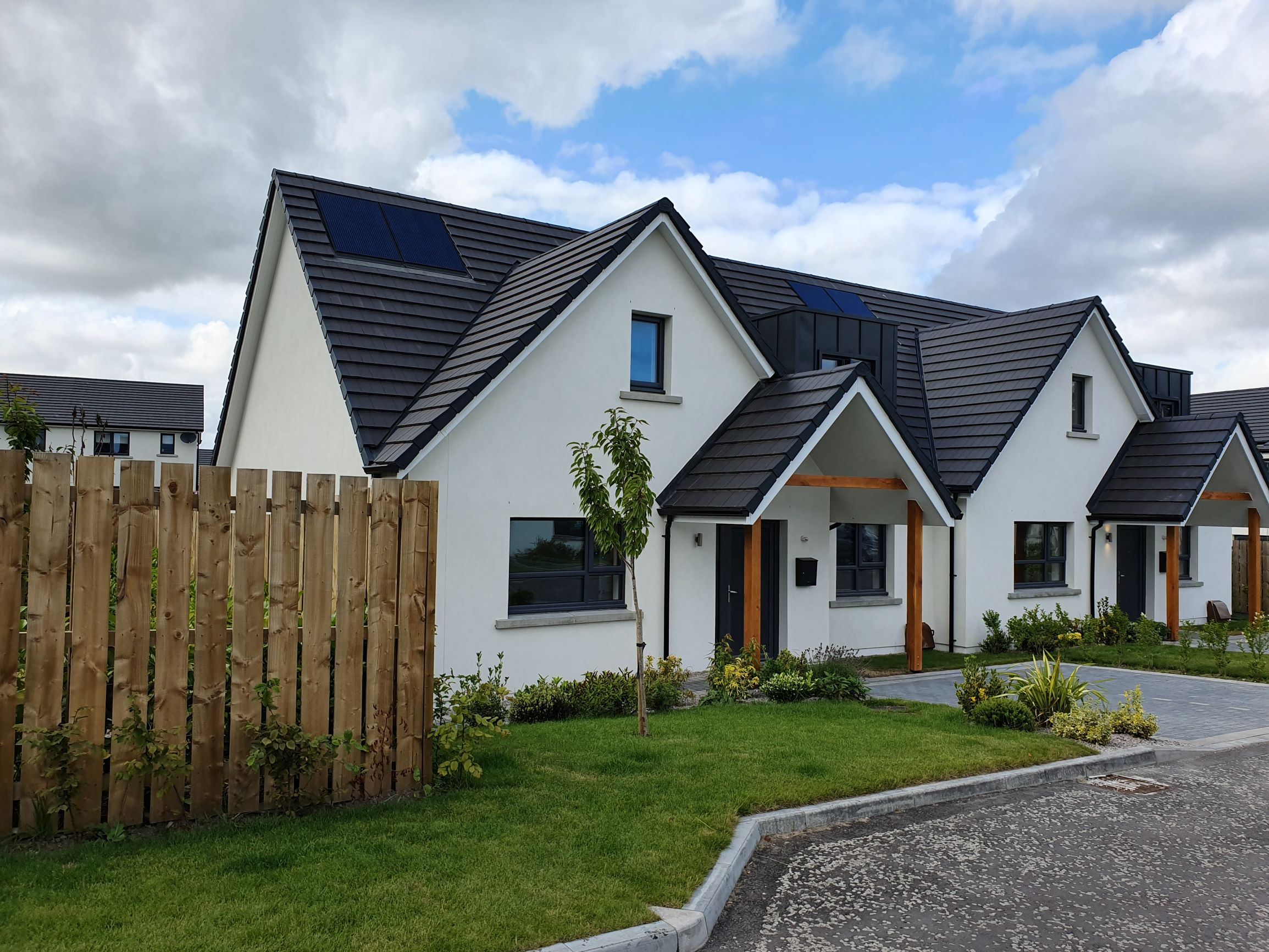
In 2016 housebuilder Dandara was awarded a BE-ST grant to fund research into whether volume housebuilders could design and build to Passivhaus standard using a Scottish supply chain.
Working alongside Robert Gordon University (RGU) in Aberdeen, Dandara aimed to develop a new product: the Scottish Passivhaus model.
In 2015, when this project began, the Scottish Government had set targets of reducing carbon emissions by 42% by 2020, which was having a significant impact on how the construction industry was thinking about and approaching current and future works.
In the UK’s domestic housebuilding sector, for example, volume-build housing accounted at the time for around 90 per cent of new dwellings built. Properties were being produced to low-carbon standards, but not to the coordinated design and quality assurance standard of Passivhaus or equivalent. Scottish companies has been slow in comparison to equivalents to pursue the benefits offered by developing components and systems for the low energy sector. The Dandara/RGU project aimed to create a deeper understanding and market adoption of an ‘affordable Passivhaus’ standard based on establishing, as far as possible, a Scottish-based supply chain. One would be built to to Passivhaus standard, using certified Passivhaus products and processes, and one created to the ‘Scottish Passivhaus’ standard.
As well as establishing whether a Scottish supply chain could be created, this would identify technical and project management modifications needed to achieve compliance, and allow Dandara effectively to cost future builds created to emerging regulatory standards. Two homes would be built as part of the project: one to approved and certified Passivhaus standards and one that would replicate the process using locally-sourced components and materials wherever they were available. As well as assessing effectiveness and affordability, the project would seek to maximise employment of local companies along the supply chain and help them gain Passivhaus certification for their products. It would also examine the benefits of the Passivhaus build for occupants, not only in terms of reduced energy bills but also as they relate to comfort and health.
90
%
less energy than standard build
meaning reduced CO2 and bills
Passivhaus standards can be applied to provide high-quality housing at a competitive cost level, utilising the local Scottish supply chain and taken to mass market.
The project would focus on Dandara’s Hazelwood development in Aberdeen. The ‘Rowan’ home type was selected for adaptation as a representative of a standard home in terms of specification, buildability, build cost, energy efficiency, running cost and open market value. One would be built to Passivhaus standard, using certified Passivhaus products and processes, and one would be created to the ‘Scottish Passivhaus’ standard.
Both homes utilised a timber frame designed and manufactured in Scotland, and erected by a locally-based timber frame installer.
Passivhaus standards can be applied to provide high-quality housing at a competitive cost level, utilising the local Scottish supply chain and taken to mass market. Project hypothesis
- Dandara
- Robert Gordon University
- BE-ST
- Scotframe
This case study was prepared by BE-ST on behalf of the Scottish Construction Leadership Forum.