Content
A-Z Circular Economy Award Winner: Kenoteq
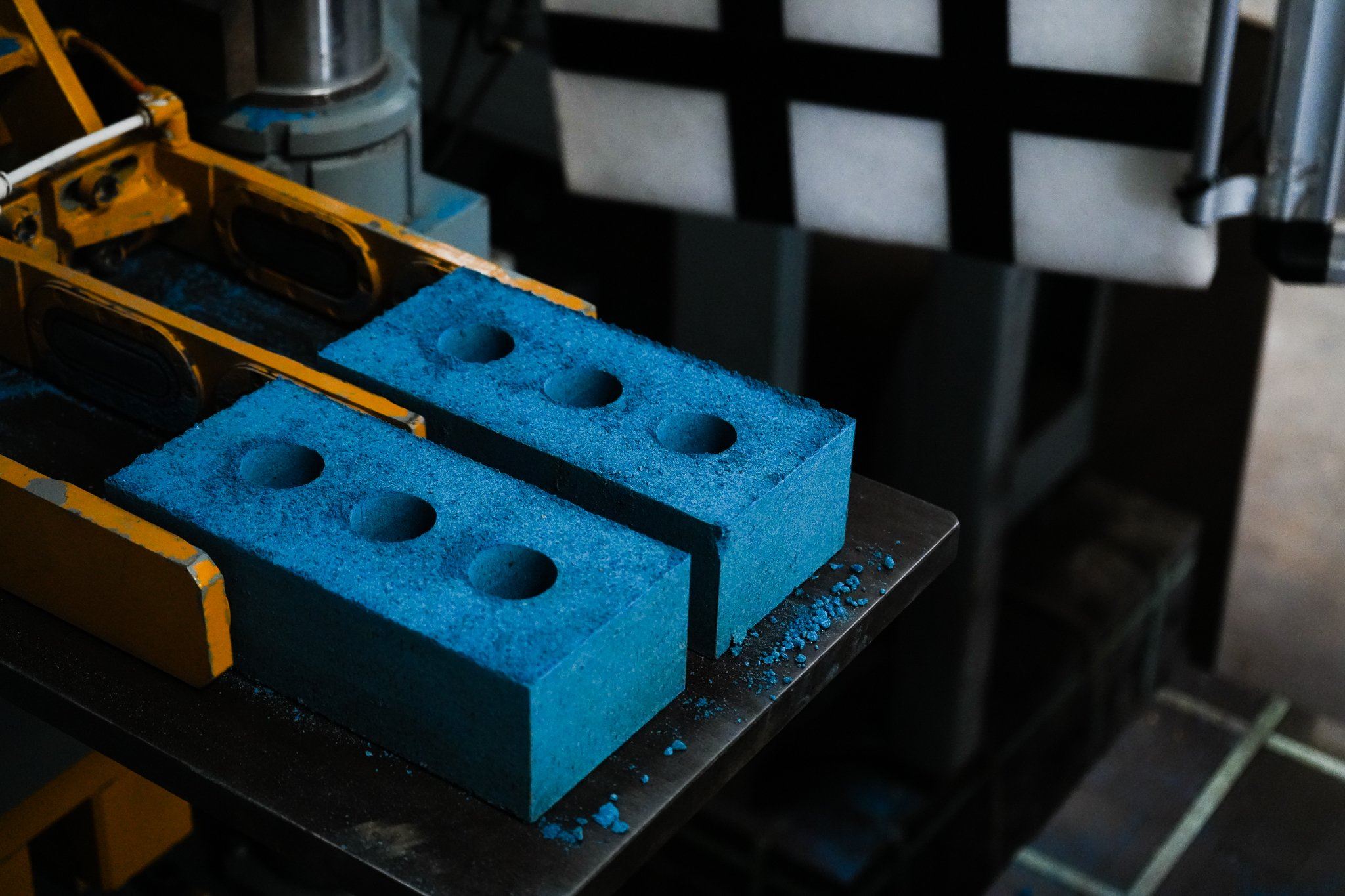
Kenoteq is the company behind the world’s first 95% recycled brick, the K-Briq. This disruptive brick turns old construction waste into a new ultra-low carbon construction material, while still having the strength, durability and workability to fit in well back on construction sites.
The result of an academic-industry collaboration between Hamilton Waste and Recycling and Heriot Watt University, the spin-out company has gained international attention for its impressive circular approach, with plans of rolling it out across the UK and internationally through local regional hubs.
The company also won our Accelerate to Zero Built Environment Circular Economy Award, recognising their work in creating a product that has circularity at its core.
The K-briq’s journey so far
Sam Chapman, co-founder of Kenoteq, and Lucy Black, Kentoeq’s Head of Business Development, sat down to tell us about the company’s developments with the K-Briq over the last few years, their pipeline of projects, and how the K-Briq’s circular approach extends to supporting a just transition across the country.
The K-Briq started as the brainchild of Dr Sam Chapman and Professor Gabriela Medero, a research project invented in the university lab with the goal of making an ultra-low carbon brick that uses construction and demolition waste. Collaborating with industry partner, Hamilton Waste & Recycling, this came as part of a ten-year development journey, which BE-ST supported along the way from 2018.
Over these ten years, the mission continued to grow.
The pair set up Kenoteq as a spin-out commercial entity to bring the product to the construction sector and built environment. They engaged with two recycling facilities close to their initial pilot factory to take locally-sourced recycled waste from the construction industry to reduce local environmental impact and to keep transportation to a minimum, feeding into the circular economy and driving down embodied carbon . Kenoteq has now gone onto establish a full-scale factory in East Lothian to produce the bricks to meet future demand, partly funded through the Circular Economy Investment Fund.
This was opened in 2023 after facing delays and challenges through Covid-19 and according to Sam, has seen “a drastic increase in our capacity for production.”
The factory is capable of producing several million bricks per year. This will save up to 10,500 tonnes of waste annually – the equivalent of 1750 6-yard skips.
The Just Transition and the Scottish circular economy
Kenoteq’s circular approach doesn’t stop in East Lothian.
The company has a vision for creating local green jobs for communities elsewhere in the UK and in the future beyond, through the establishment of regional K-Briq production facilities which use local waste materials to solve local construction waste challenges as well as minimising carbon emissions, through less transportation and recycling: “Our whole scaling model is based around us setting up more regional production facilities across the UK and internationally, so you're using local waste within local projects and that keeps the transportation carbon as low as possible. You've then got the local job creation in the manufacturing and sales, and you’re supporting local supply chains within the waste processing and distribution sectors as well.”
By championing locally produced sustainable building materials, the team aims to contribute to the region's environmental goals while also supporting the local economy, a perfect combination for achieving a just transition.
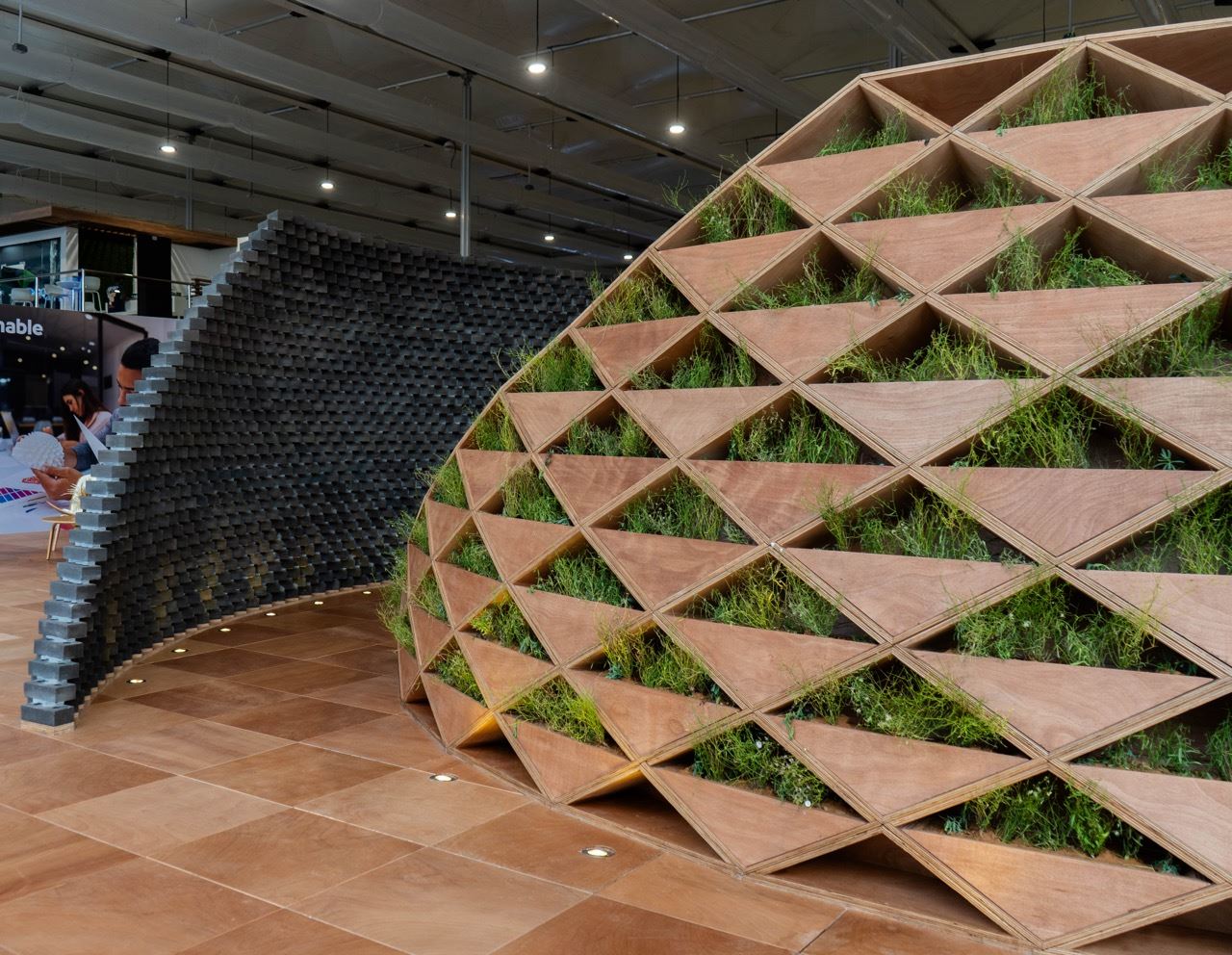
International attention
Despite challenges in commissioning their facility through Covid-19, the company has built an impressive amount of awareness and confidence in their product, attracting interest both nationally and internationally.
They have had global leading architecture practices with a firm focus on sustainability and design knocking on their doors. The brick has also gained attention from politicians such Scottish First Minister Humza Yousaf, media outlets such as Bloomberg, and was featured at the recent Conference of the People (COP28).
In our conversation, we spoke about the company’s future off the back of this positive attention: “We’ve got a really healthy pipeline of projects for 2024 and 2025.”
“Some of these are in Scotland. Some are public sector-led, others private sector-led and a great number of projects elsewhere in the UK and particularly in the City of London. City of London does have design standard carbon targets, so there's more of an incentive for projects within the City of London to be looking and adopting low carbon building materials.”
Local education
In order to help deliver these projects, Kenoteq has invested in educational programs, delivering sessions to architects, designers, engineers, apprentices, and other stakeholders to enhance understanding of their products' technical specifications and sustainability features.
“We've delivered over 200 CPD sessions to over 2,500 architects, designers, engineers, clients, and contractors over the last 18 months and that's really helped gain our understanding on a technical level. We can keep an open dialogue with clients as well as contractors and the design community.”
They also focus on bringing the next generation of builders in on the conversation: “Following some great collaborative work with Fife College, we're now working with Barnsley College to bring young people along and see the opportunity of these sustainable building materials but also helping to train the bricklayers of the future and convince them of the benefits of using the K-Briq.”
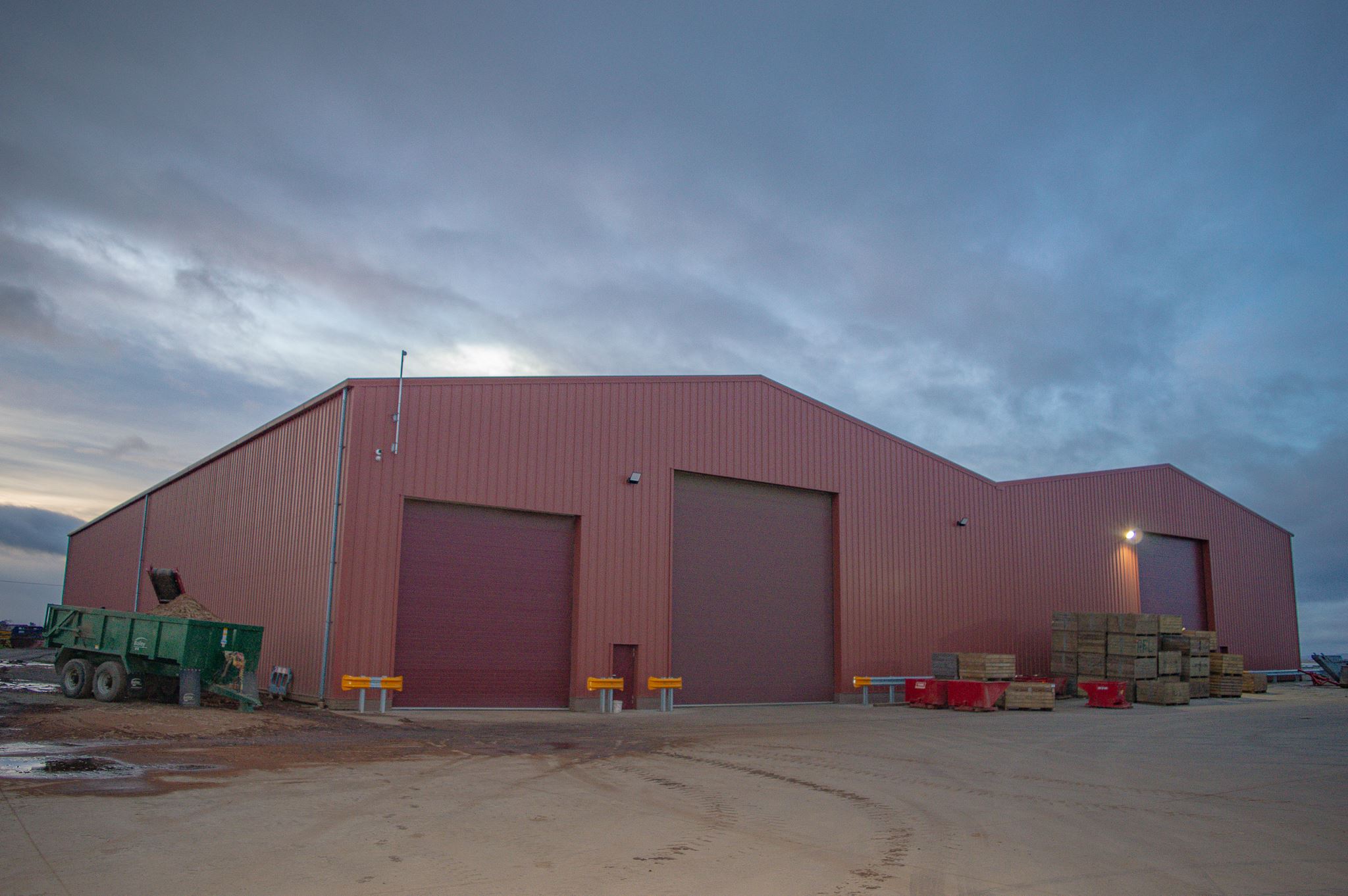
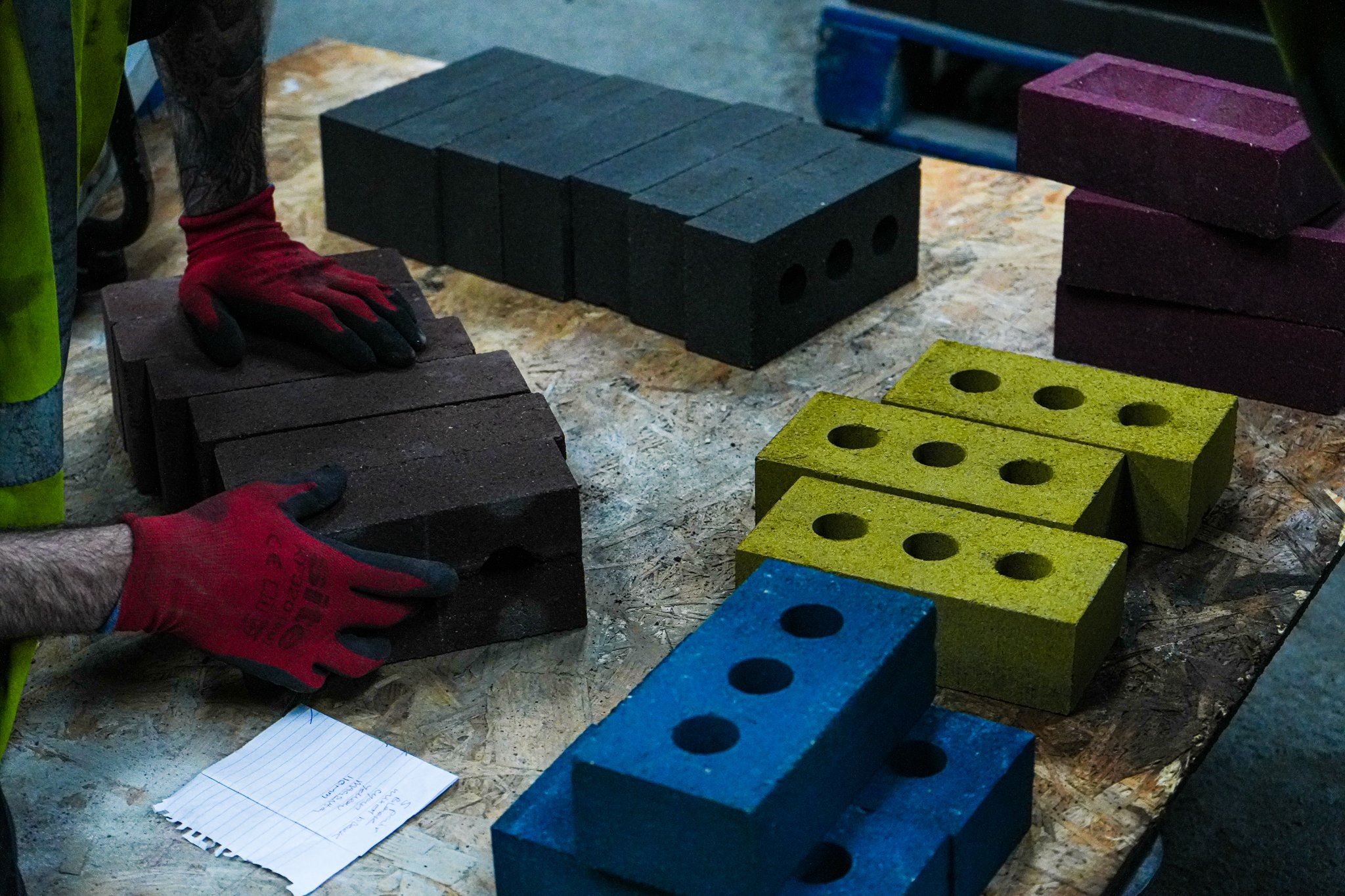
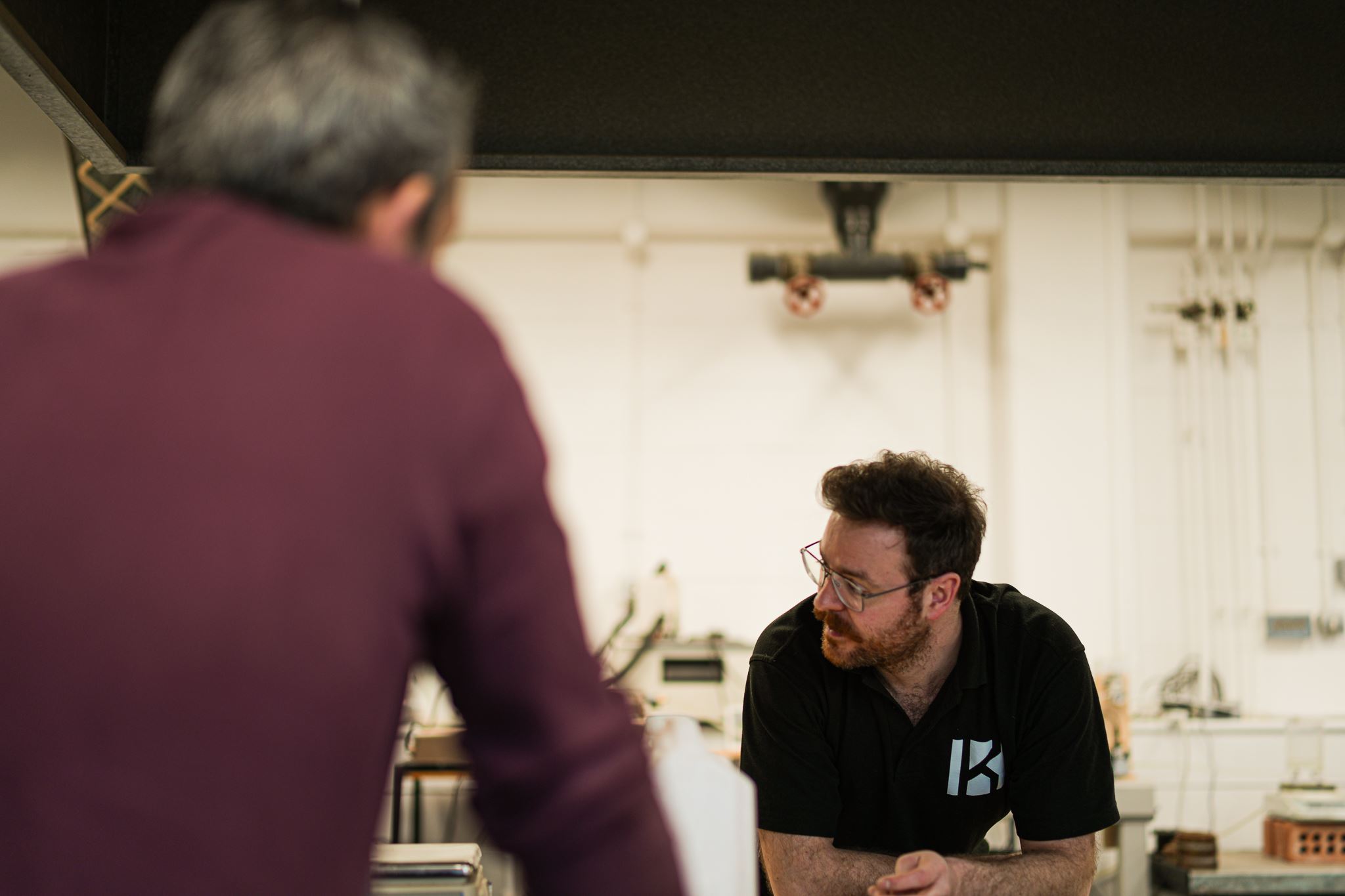
How bricklayers react to the sustainable brick
When we asked how the industry responds to the product, Sam says that bricklayers have reported finding them stronger and much easier to cut than traditional bricks.
“The biggest compliment is that it looks and acts and feels like a brick,” Sam says. “But now people are saying positively that they almost prefer working with it.”
“Coming from an academic background, we needed to learn what is it like when a bricklayer gets our product in their hand. Because it's all well-and-good selling it to the architects and the designers of this world, but if the bricklayers struggle with it, you're not going to survive very long. It's been really positive to get some of that feedback.”
What did winning the award mean to Kenoteq?
Discussing winning the Circular Economy Award, at the Accelerate to Zero Awards run by BE-ST, Sam says: “It’s further confidence for both us and the industry in an emerging sustainable low carbon building material that is local to Scotland. And I think that's very important and particularly in the just transition. We want to be driving local solutions.”
What’s next for Kenoteq?
The K-Briq continues to be used in interior projects. It is in its final stages of BBA certification in the UK allowing its commercial use in exteriors from late Spring 2024. Plans for the future include setting up regional production across the UK, finalising European and US certification to develop international markets - and delivering on their expanding pipeline of projects.
Accelerate to Zero Awards 2024
Interested in being involved in this year’s Accelerate to Zero awards, either as a sponsor, applicant or attendee at the awards?